How Cigars Are Made
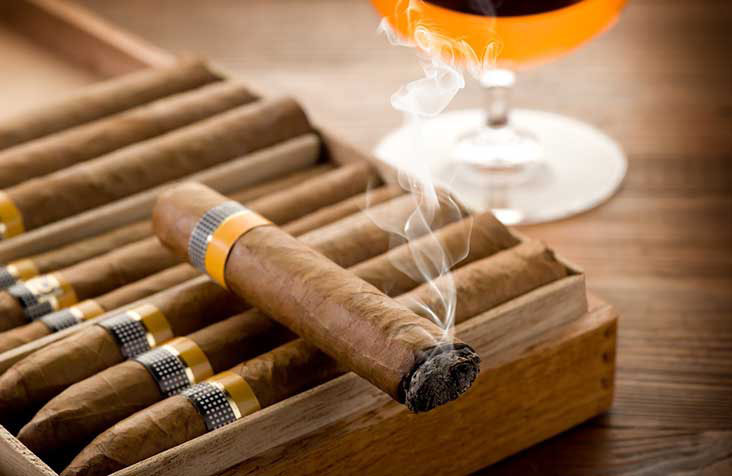
Cigars are enjoyed by many people all over the world and it is a booming industry that is expected to grow with each passing year. Cigars are renowned for the luxurious smell and aroma. There are many family companies that have made cigars for generations. One such company is AJ Fernandez Cigars. They pride themselves on producing the finest quality cigars.
The first people believed to have smoked cigars are the native tribe of the Mayans in South America. The word cigar was developed from the word sikar, which to the Mayans means to smoke tobacco rolled in leaves. The word eventually became cigar with the culmination of the Spanish word cigarro. The history of the cigar is rich with interesting facts, and the process of how cigars are made is equally fascinating.
The Cigar-Making Process:
Growing The Tabaco
Growing tobacco is the first step in the process. This can take up to 10 weeks. The seeds are best cultivated in a warm climate like Africa, South America and the Caribbean. AJ Fernandez Cigars are produced in Nicaragua and are the largest manufacturer there, selling almost 9 million a year. After the tobacco grows, it must mature and age in the fields for several months.
Harvesting & Fermenting The Tabaco
During harvest time, the leaves are finished and ready to be cured when they have become very dry and brown in color. During this process, the cigars are strung into shapes that are called laths which are hung to dry in a curing barn. After the curing process, they are separated and split up according to size or color. The plants undergo a fermenting process anywhere between 6 months to several years. It is during the fermentation period that the tobacco gets its distinct aroma and taste.
Stripping The Tabaco
The leaves then have the stem removed so that they can burn evenly. This step is called stripping. Once stripped, they are further fermented and steamed. This restores any lost moisture that occurred during the fermentation.
Wrapping and Rolling The Tabaco
Now the cigars are ready to be wrapped and rolled. It must be done perfectly in order for the cigars to burn appropriately. A special kind of knife is used when removing any imperfections in the roll. They are wrapped and rolled in the wrapper leaf several times and closed with a vegetable paste.
Usually, a machine is required now to finish the rolling process, ensuring that everything is even and cut into the proper size. After they are rolled, they are inspected carefully and labeled with information, such as the type of tobacco, the cigar maker or size.
After the inspection is completed, the cigars are stored in large cedar bins and put in a room where the humidity is distributed evenly. They are stored anywhere from weeks to years in the room. Once they begin to dry and shrink here, they become richer and develop a slower burning process for the consumer. With all these cedar bins stored in the same room, the tobacco is allowed to absorb any aroma and seasoning it comes into contact with. Eventually, all the cigars will become alike in smell and taste.
The production and marketing of every brand of cigar is different, and each may have their own trade secrets for developing the taste of their unique cigars. The AJ Fernandez Cigars company sells its products in over 32 different countries and continues to have success at becoming one of the top cigar manufacturers.